The utilization of rare earth magnets in vehicle traction motors has become common, in particular that of the rare earth-based, hard magnetic materials. But their price has significantly increased over the past few years, which worries the manufacturers of hybrid and electric vehicles. Additionally, there are specific limitations to the performance of electrical machines which use such materials:
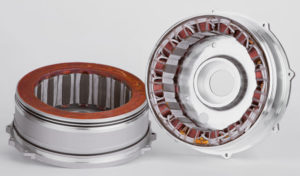
- Maximum operating temperature is limited to 120-150C
- During rotation, magnetically induced voltages are always present on the motor terminals which causes problems in case of a short circuit in the windings)
- At high speeds the back EMF becomes so large that it exceeds the available motor supply voltage, inducing additional currents into the motor windings and weakening performance of the motor
- A loss of energy occurs even when the motor is de-energized.
- Presence of cogging torque (which results in noise, vibration and rougher operation in electric drive systems).
- Motor’s magnetic field weakens with time.
- Magnets can be demagnetized by excessively high currents.
- The rotor of the motor is sensitive to ferromagnetic dust.
The simplicity and robustness of the asynchronous motors makes them attractive for traction applications but they have some problems of their own:
- Heat dissipation in the rotor (which makes it difficult to cool the rotor in high density motors)
- lower efficiency compared to other types of motors
- Lower starting torque
The Switched Reluctance Traction Motors (SRTM) without NdFeB materials or windings on the rotor, having significantly higher reliability, lower material cost, become the prime choice for the traction drives in electric or hybrid vehicles.
The SR machine was the first electric motor to have been designed but until the last two decades hasn’t been successfully implemented. The reasons deal primarily with controller and power switching components. The constantly changing magnetic field is highly non-linear, the torque ripple is high at low speeds, position sensors complicate the design. Earlier implementations were noisy, unreliable, controllers were expensive due to high cost of electronic components. However, most of these difficulties can be overcome by using modern CAD and simulation software, digital signal processors which today are faster but cost much less, new power switching components, and by developing specialized hardware and sophisticated algorithms and models.
And this is where KASKOD-MTRONIX comes in. Our lead engineers have extensive experience with digital signal processing and power circuits spanning over two decades, as well as with microprocessor control, embedded systems, mechanical design, user interface, communications buses and secure remote control solutions.